Have you spent years mastering the art of string playing but still know little about the ideal way to handle your tools? Are you curious to learn more about the possibilities a high-performance string offers and do you want to optimize your performance in a few simple steps? Stringtelligence offers you an exclusive insight into the science of strings. Find widely unknown tips and tricks of the trade to perfect your sound and elevate your playing to an unexpected level! More than 20,000 words and 19 video tutorials in over 90 chapters: This is string know-how at its best!
How is a string made?
Strings are state-of-the-art, high-tech products – a combination of physics, mathematics, material science, corrosion science, precision machining and tool design. Thomastik-Infeld has been researching, developing, building and producing for a hundred years now. We want to provide you with an insight into our processes and show you the broad stages of developing a string.
The task: a violin A-string.
The note (440 Hz) and the vibrating string length (32.5 cm) are predefined.
1. Defining the desired string tension
First, the designed string tension is determined. Thomastik-Infeld strives to make the string tension as low as possible, but as high as necessary. Why? Too little string tension would lead to a nasal sound and too little resilience of the string. This means: at a low volume, the string would be pressed to the fingerboard too quickly and would rattle, the string sound would crack in the event of a higher load, etc. Too much string tension would lead to the instrument being overloaded. This would cause the loss of sound colors and overtones and a trumpet-like sound would occur.
The core must also withstand the desired string tension. When we define a string tension of 5.50 kg, the core must support a load of at least 5.5 kg without any problems. The string tension defines the mass that is necessary to tune the string to the keynote. Thomastik-Infeld attaches the highest importance to safety and reliability. For this reason, an additional safety factor, a buffer, is included, so that the string doesn’t snap in the event of a higher load. This is very similar to a cable car, which must never snap, even if the load is higher than stipulated.
The string tension results from the mass per unit of length (mass of the string in the vibrating string length). As an example: to achieve the string tension with the fictitious value of X, 10 grams per meter are required. In the end, the total sum of the masses of all the materials used must be 10 g/m. When selecting the individual materials, this must be meticulously considered.
There are now three specifications: the note, the vibrating string length and the string tension.
2. The detailed definition of the characteristics that the string should have comes next:
- Tonal character (brilliance and warmth)
- Tonal diversity (rich and complex or pure)
- Sound beam when playing (broad or focused)
- Honesty of the string (the string drowns out the instrument or emphasizes the individual character of the instrument)
- Dynamic range: pressure applied by bow (maximum load capacity in fortissimo, confident response in pianissimo)
- Dynamic range: volume & audibility for the player (to the ear), power & projection for the audience (3 P to 3 F)
- Modulation (forgiving versus modulatable)
- Volume modulation (quiet and loud)
- Tonal break-in time (metallic sound, sounds following string change)
- Pitch stability
- Life span of winding (corrosion resistance, abrasion resistance, etc.)
- Response when shifting the left hand
- Bow response
- Left-hand feeling (Soft versus Firm)
- Right-hand feeling when bowing (Soft versus Hard)
- Solution in case of problems such as wolf tone, buzzing, whistling
3. This results in the search for the right materials and their combinations, always under the proviso of complying with the relevant total mass. And now the construction of the string begins.
First, we choose the core material: synthetics (polyamides such as nylon or perlon, polyester or a wide range of polyaryletherketones), chromium steel (unplated or plated) or carbon steel (as a wire or rope). The core material bears the string tension, provides the tonal and haptic direction and has a certain weight (mass per length). Synthetics, for example, have 1.6-2 g/cm3, while steel has 7.3-7.8 g/cm3.
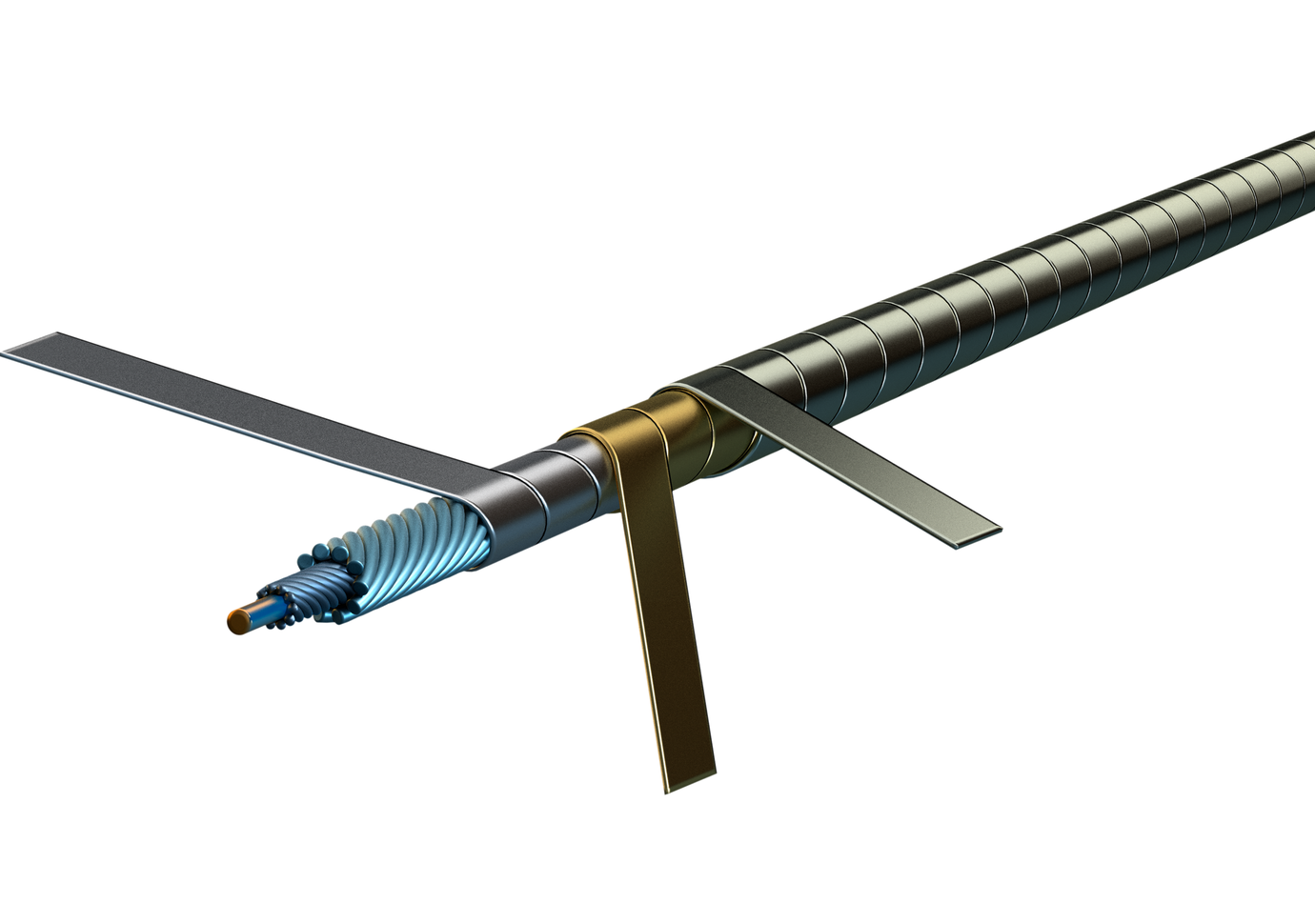
With the exception of the plain string (e.g. violin E-string, descant strings for guitar), Thomastik-Infeld strings are made up of a number of layers. According to the desired sound and handling characteristics, we then choose a surface material (material of the outermost layer). Next we select the type and number of layers and the material for the inner layers. We decide between round wire and flat strips and determine how many strips and wires are wound in parallel, i.e. simultaneously. Proviso: mass per length.
This naturally produces limitations and challenges. The higher the density and the diameter of the core, the less can be applied to the outside, so that the mass per length unit corresponds exactly to the specifications.
The higher the string should sound, the less overall mass it should have. M (mass) = (density) x V (volume). The higher the density of a material, the less volume is required to achieve the same mass. For example, silver has a very high density, with 10.5 g/cm3. On the other hand, aluminum has a density of 2.6 g/cm3. This means that significantly more aluminum (greater band thickness) than silver (smaller band thickness) can be applied to achieve the same mass.
WINDING MATERIAL | DENSITY | |
ALUMINUM | 2.7 g/cm3 | light-weight material |
TITANIUM | 4.5 g/cm3 | light-weight material |
CHROMIUM STEEL | 7.9 g/cm3 | heavy-weight material |
NICKEL | 8.9 g/cm3 | heavy-weight material |
SILVER | 10.5 g/cm3 | heavy-weight material |
GOLD | 19.3 g/cm3 | heavy-weight material |
TUNGSTEN | 19.3 g/cm3 | heavy-weight material |
Naturally, you could now wind a very small amount of silver around the string. However, this would not produce any mechanical stability as the band would be extremely thin. You need to achieve a certain band thickness to guarantee the mechanical stability of the winding. This also needs to be taken into consideration when choosing the winding materials.
The consistency and stiffness of the materials used also needs to be considered, along with the thickness. For example, a wound violin E-string with a string tension of 7.7 kg has a carbon steel core with a diameter of 0.22 mm. To achieve this string tension, you wind this core with an aluminum band (2.7 g/cm3) with a thickness of approx. 0.04 mm. If this string were wound with a chromium steel band (7.9 g/cm3) instead, it would have a thickness of approx. 0.013 mm, i.e. a third. With a silver band, this would actually only be a quarter of the thickness. Chromium steel is a very stable, solid material. For this reason, you can produce chromium steel-wound E-strings despite the minimal thickness. Silver, on the other hand, is a soft material and would quickly incur damage in the event of stress. As a result, Violin A- and E-strings as well as viola A-strings are not produced with silver winding.
Thomastik-Infeld works with its own high-precision rollers, which are developed and built in-house. These produce bands with an accuracy of up to 0.5 micrometers (0.0005 millimeters). Just as is the case in sports, these figures quite simply make the difference and elevate us to number one. After 214 kilometers and about five hours of riding time, Marcel Kittel won the Tour de France 2017 with just a 0.0003 second lead (with an average speed of 70 km/h, this corresponds to about 6 mm). A little fun fact: Thomastik-Infeld was one of the main developers of the Bowden cable for bicycles.
Back to the string: for very high sounding strings, like violin E- and A-strings as well as viola A-strings, the mass of the core determines the predominant part of the total mass. This means you can only apply a very slight amount of winding mass. This is another reason why certain strings, e.g. silver-wound violin E- and A- strings as well as silver-wound viola A-strings don’t exist.
The end:
The time to produce a single string takes between 1,5 to 10 minutes. But developing it can take up to 2 years. The first prototype strings are tested, improved and refined until the predefined result is met and until the string meets our standards of quality.
BACK