Have you spent years mastering the art of string playing but still know little about the ideal way to handle your tools? Are you curious to learn more about the possibilities a high-performance string offers and do you want to optimize your performance in a few simple steps? Stringtelligence offers you an exclusive insight into the science of strings. Find widely unknown tips and tricks of the trade to perfect your sound and elevate your playing to an unexpected level! More than 20,000 words and 19 video tutorials in over 90 chapters: This is string know-how at its best!
What needs to be considered when mixing strings?
If you decide to combine strings from different product lines, six factors should be kept in mind in order to ensure optimum results:
1. Core material:
Core materials can be mixed within a combined set of strings. That means that it is feasible, for example, to replace a synthetic core A- with a steel core A-string on violins or violas. More information: Is it possible to combine strings from different manufacturers?
2. String tension:
If you have already found the ideal string tension for your instrument, you should definitely stick to it – not just overall, but actually per individual string. If you do not yet know the ideal string tension for your instrument, the combining of different strings with varying string tensions provides a way to test this and thus reach the optimum outcome. Don’t forget: beware of signs of overloading and underloading! Further information about string tension and its importance can be found here: What is string tension? and How does the string tension affect the sound and the instrument?
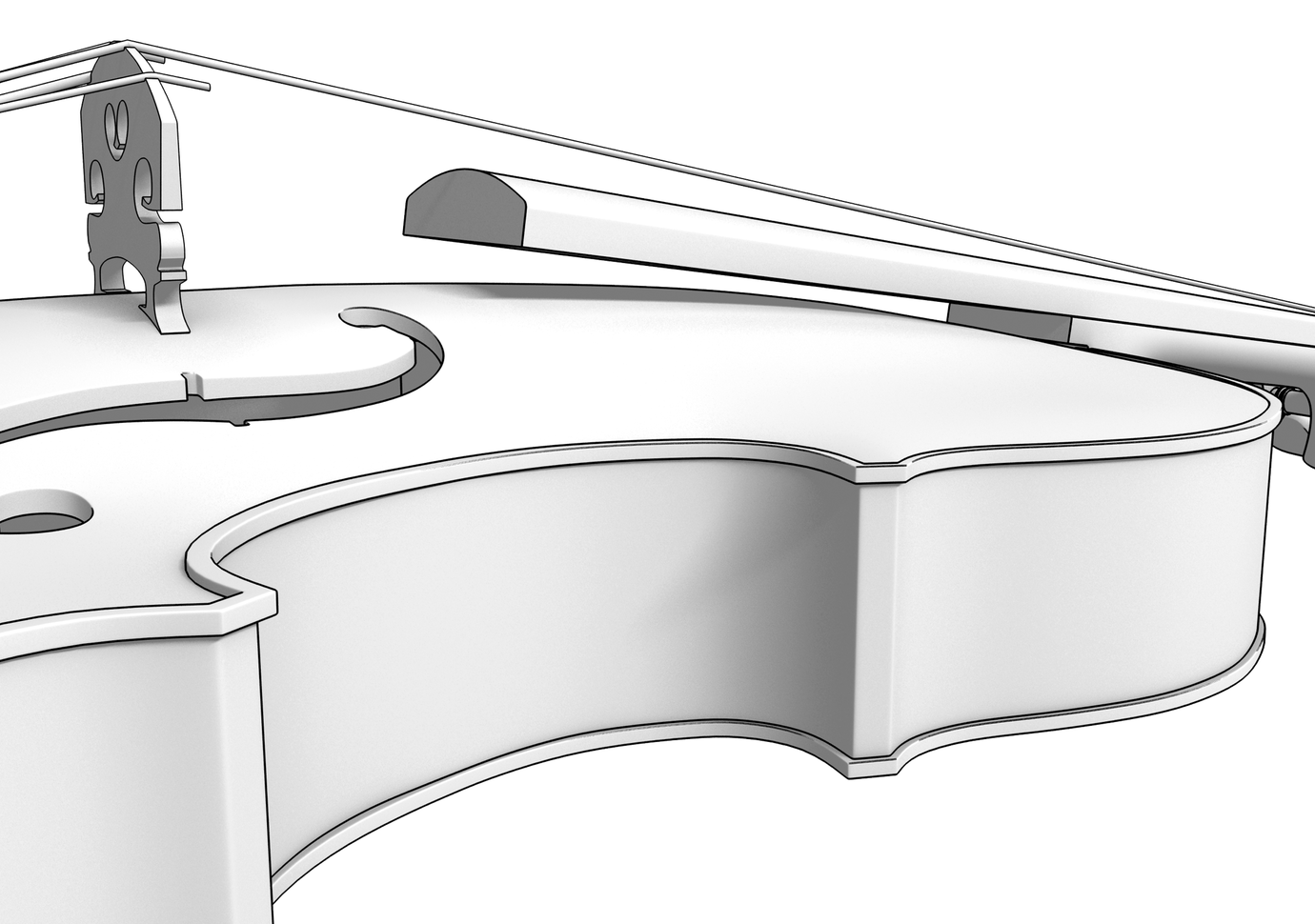
3. String action:
The string action is the distance from the string to the fingerboard. Alongside the string tension, the action is also important for the sound and the handling of the instrument. Depending on the string tension of the open string (not played), the elastic modulus and the distance to the fingerboard, more or less force is required to press the string down onto the fingerboard. The higher the modulus of elasticity and the string tension, the lower the distance between the fingerboard and the string. Steel core strings have a high modulus of elasticity, synthetic core strings have a low modulus of elasticity. Generally speaking, instruments with a very small string action (minimal distance between strings and fingerboard) require the use of strings with higher string tension or steel core strings (due to the modulus of elasticity), in order to achieve an ideal response and left hand as well as bow hand feeling (handling). If a string with a low string tension or a string with a low modulus of elasticity is used on an instrument with a small action, the string touches the fingerboard too fast under the pressure of the fingers or the bow, and thus is prone to rattling. However, caution is advised when selecting a string with higher tension! This could have the effect of overloading the instrument. A more beneficial and “healthier” alternative for the instrument is to have the string action adjusted by a luthier.
4. WINDING MATERIAL:
Different winding materials have different effects on diameter, bow response, bow noise, left-hand feeling (sliding feel), sound, volume and corrosion.
WINDING | DIAMTER | BOW RESPONSE | BOW NOISE | SLIDING FEEL | SOUND | VOLUME | CORROSION RESISTANCE | BRILLIANCE | FLATTENING EFFECT |
ALUMINUM | greater | better | stronger | average | more brilliant | average | lower | higher | lower |
SILVER | smaller | average | average | increased | average | lower | average | average | average |
CHROMIUM STEEL | average | inferior | lower | reduced | darker | louder | higher | lower | higher |
5. String diameter:
The diameter of the string influences the left-hand feeling and the bow response. A major misconception is that thinner strings – meaning those with a smaller diameter – always have a better response than thicker strings. This is correct if the strings you are comparing have the same core and external winding material and the same string tension. However, if these characteristics differ, it’s no longer possible to make this assumption.
WINDING | DIAMETER | BOW RESPONSE | SLIDING FEEL |
ALUMINUM | greater | better | average |
SILVER | smaller | average | greater |
CHROMIUM STEEL | average | inferior | reduced |
6. Pitch stability and tonal break-in time:
Sets of strings are put together not only on the basis of their tonal lifespan and characteristics, but also under the condition that they achieve their pitch stability and tonal development in as simultaneous a manner as possible. Therefore, if one combines strings from different families, it can take differing lengths of time until the individual strings have reached a stable pitch and have unfolded their full sound potential.
Both steel wire and steel rope core strings generally achieve pitch stability right away and thus much faster than other core materials (violin steel core E- or viola steel core A-string). As a result, they can be easily combined with other strings when it comes to the point of pitch stability.
This is not to be confused with the tonal break-in time (= the time a string needs until all tonal colors have fully developed and the metallic sound component and background noise have disappeared), as this can take significantly longer with steel core strings. This means that even if all four individually combined strings of different product lines have already reached pitch stability and can be played smoothly, they may still require varying amounts of time until all of them have unfolded their full sound potential.
BACK